Abstract
A more accurate name is MgO cement or Magnesium Oxide Cement. The magnesium oxide cement family has three types:
Magnesium Oxychloride or MOC

MOC is made by reacting magnesium oxide and magnesium chloride, an extremely hygroscopic material. Some MOC products can be very corrosive to nails and screws and absorb moisture from air. All MOC products release highly toxic and corrosive hydrochloric acid gas when exposed to fire. Some imported products are based on MOC.
Avoid this product at all cost!
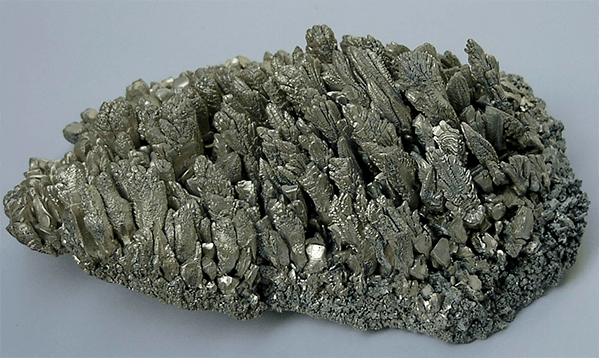
Magnesium Oxysulfate or MOS cement

Magnesium Oxysulfate or MOS cement is a non-hydraulic cementitious material. It is formed by mixing a suitable proportion of magnesium oxide (MgO) powder with a concentrated magnesium sulfate (MgSO4) solution. MOS cement hardens rapidly and has excellent mechanical performance, low thermal conductivity, good abrasion resistance and good chemical resistance.
Therefore, it can be used as a fireproof material, reinforcement additive, and building material. This product combines the best performance properties with ease of processing and reasonable cost. Our product is 100% MOS. It is non-corrosive, strong, and does not release toxic fumes when tested at 1800 oF according to ASTM E-119.
Magnesium Phosphate

This family of magnesium oxide cement is very expensive and difficult to make due to the extremely high reactivity.
Introduction
A well-made magnesium oxide cement product has many advantages over conventional building materials.
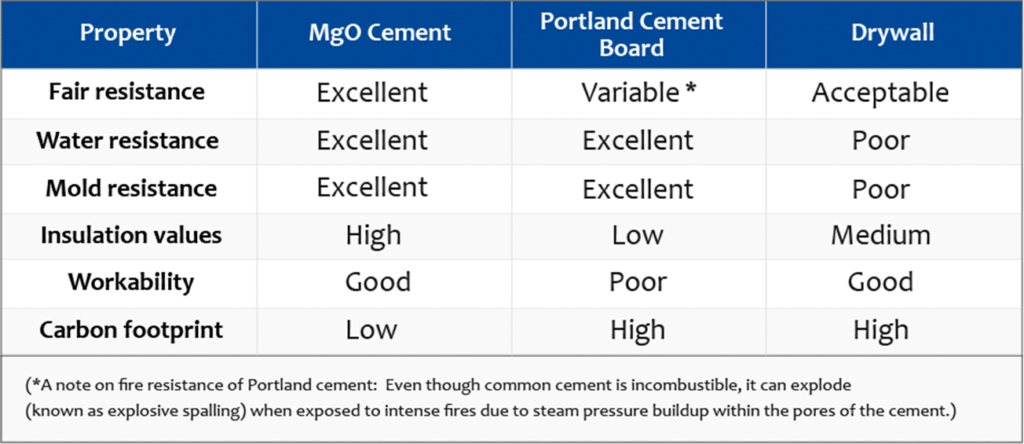
The benefits MgO can only be realized by careful execution of every step of the process. Making MgO cement materials requires exact science. The formation of magnesium oxide cement involves a chemical reaction to form the desirable crystal form known as the 517-phase. Our products are different from any other MgO products on the market.
Starting with a patented formulation and process, we ensure that all parameters are optimized for the highest 517-phase content. Since raw materials vary from batch to batch, we adjust our formulation according to real-time analysis of every batch of raw materials.
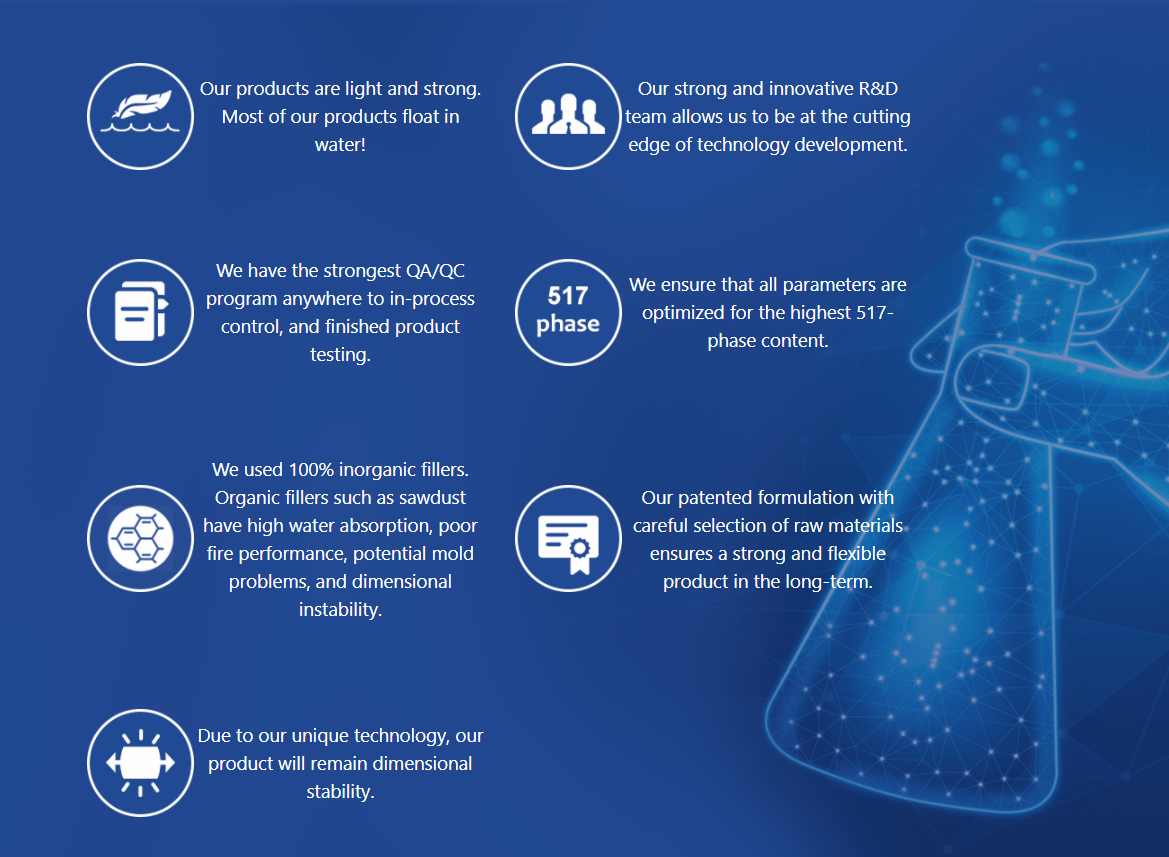
History
MgO was first discovered by French Chemist Stanislas Sorel in 1867 when it then became known as Sorel Cement but Magnesia has been used in construction for centuries.
- Magnesia cement uses in masonry construction is ancient. It was used primarily as a mortar component and stabilizer for soil bricks. Magnesia has also been identified in the Great Wall of China and other ancient landmarks. Roman cement is reported to have contained high levels of magnesia.
- In the West, Portland cement replaced magnesia for masonry uses in the 20th century when energy was cheap and mold infection was poorly understood.
- However, some projects continued to use magnesia. New York City’s Brooklyn Bridge base is made from locally mined cement, a mixture of calcium oxide and magnesia cement commonly called Rosendale cement, the only natural non-fired cement made in the US.
- Magnesia cement boards were approved for construction use in the US around 2003.
- Due to its fire resistance and safety ratings, New York and New Jersey were early adopters of magnesia cement board. Florida has adopted magnesia boards for mold/mildew resistance. It is hurricane and impact tested and approved in Miami-Dade County.
- Located in Taipei, Taiwan, magnesia board can be found on all 101 stories of Taipei 101, currently the eighth tallest building in the world. Magnesia sheeting was used on the inside and outside of all the walls, fireproofing beams and as the sub-floor sheathing.
Composition & Structure
The set cement consists chiefly of a mixture of magnesium oxychlorides and magnesium hydroxide in varying proportions, depending on the initial cement formulation, setting time, and other variables. The main stable oxychlorides at ambient temperature are the so-called “phase 3” and “phase 5”, whose formulas can be written as
respectively; or, equivalently,
Phase 5 crystallizes mainly as long needles which are actually rolled-up sheets. These interlocking needles give the cement its strength.

- The 517 phase is the main contributor for strength, fire resistance, and other attributes
- Raw material quality and formulations must be optimized for maximum 517 formation
- Curing temperature and humidity must ensure optimum crystal formation
Properties
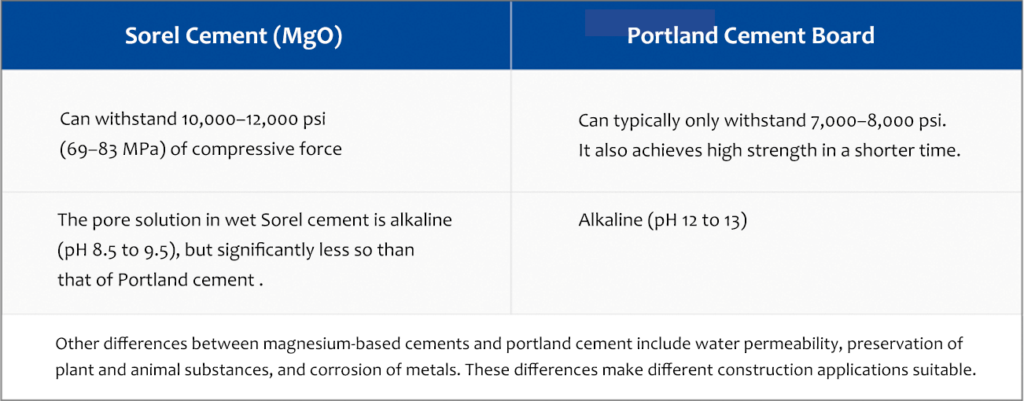
Magnesite and dolomite are both abundant raw materials however their manufacture into cements has been limited in the West due to limited markets. Its widespread acceptance and use for building board in China, has made this country the dominant supplier of raw materials. In the west, magnesium based cements are relatively expensive but only because of the relatively high cost of the magnesium oxide raw material compared to portland-cement based concrete outside Asia.
Applications
MgO is prized as a refractory material, i.e. a solid that is physically and chemically stable at high temperatures. It has two useful attributes: low thermal conductivity and low electrical conductivity. Filling the spiral Calrod range top heating elements on kitchen electric stoves is a major use. “By far the largest consumer of magnesia worldwide is the refractory industry, which consumed about 56 % of the magnesia in the United States in 2004, the remaining 44 % being used in agricultural, chemical, construction, environmental, and other industrial applications.”MgO is used as a basic refractory material for crucibles.
- Interior wall and ceiling board
- Exterior sheathing
- Trim materials
- Fascias
- Soffits
- Shaft-liner and area separation wall board
- Tile backing (backer board) and underlayment
- Substrates for coatings and insulated systems such as direct-applied finish systems, EIFS, SIPS, Portland type stucco and synthetic stuccos.
It is a principal fireproofing ingredient in construction materials. As a construction material, magnesium oxide wallboards have several attractive characteristics:

FAST, NO SKILLED LABOR REQUIRED

IMPERVIOUS TO WATER

WIND RESISTANT

FIRE RESISTANT

LIGHT WEIGHT

HIGH INSULATION VALUES

NO CEMENT OR REBAR NEEDED

SEISMIC RESISTANT

INORGANIC

NON-TOXIC
Magnesia is also widely used primarily as wallboard alternative to conventional gypsum-based drywall and plywoods. The magnesia boards can be scored and snapped, sawed, drilled, and fastened to wood or steel framing. Magnesia boards are a good example of the advances made in construction materials to meet changes in building codes for safety and durability.